This High-Performance Practical Hydraulic Drive and Controlled Trainer is a professional platform designed for hydraulic circuit experiments, hydraulic application training, and curriculum design. Ideal for colleges and vocational schools, it is tailored for training and assessment in hydraulic drive and control disciplines. Equipped with various industrial-grade hydraulic components and modules, this trainer supports comprehensive teaching and training in:
- Composition of hydraulic transmission systems.
- Basic hydraulic circuit experiments.
- Performance testing of common hydraulic components.
- Integrated control experiments.
- User-Friendly Design: The training panel features a T-slot design, allowing for easy insertion of all hydraulic components using rapid joints.
- Industrial-Grade Components: All hydraulic components and valves are industrial-grade, withstanding pressures up to 6.8 MPa. The system automatically relieves pressure beyond this threshold for safety.
- Modular Flexibility: The hydraulic modules are independent and easily assembled into various circuits on the T-slot panel, making it adaptable for a wide range of experiments.
- Quick and Safe Connections: Hydraulic circuits are connected using quick couplings, while the electrical control circuit uses protective training wires. Students can follow instructional guides or design their own system circuits, with up to 90 experiment variations possible.
- Versatile Control Modes: The hydraulic circuit can be controlled independently using either a relay unit or a PLC. By comparing these two control modes, students gain a deeper understanding of PLC advantages.
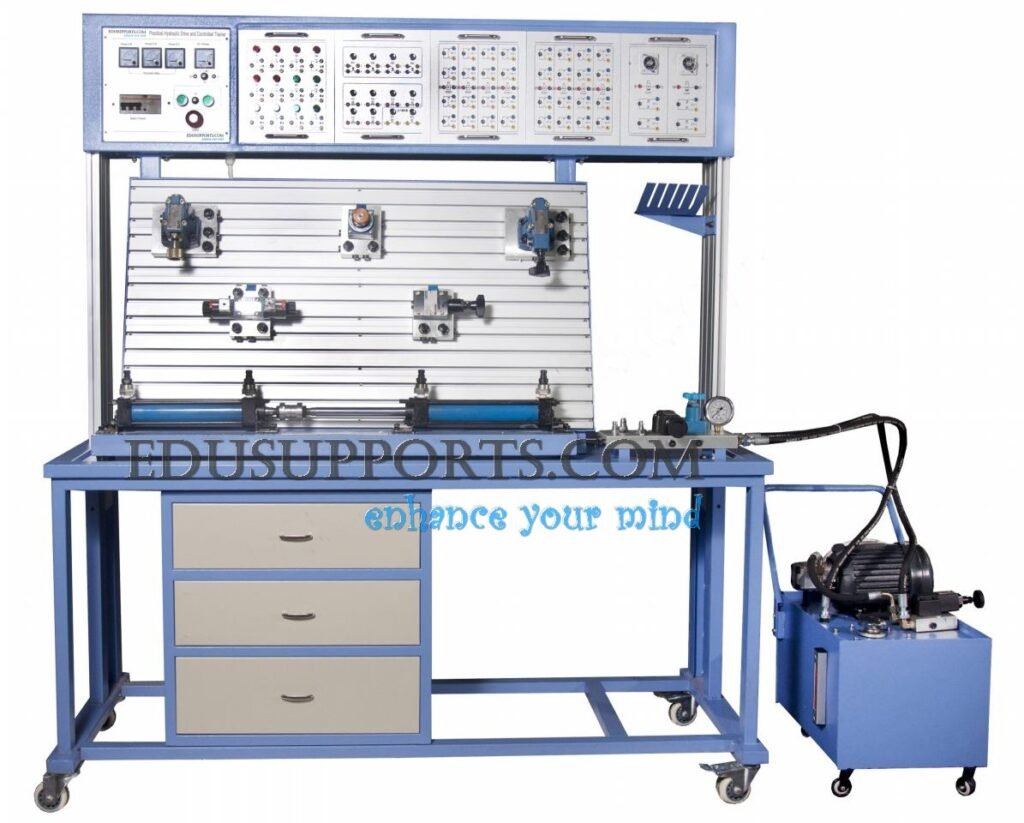
6.Enhanced Safety Features: The trainer includes current leakage protection, cutting off power if leakage exceeds 30mA. The electric control operates on DC 24V with over-current protection, preventing damage during malfunctions.
Part A: Hydraulic Circuit Training
- Pressure Control Circuits
- 1 Pressure Regulated Circuits
- Single-Stage Pressure Regulated Circuit
- Two-Stage Pressure Regulated Circuit
- Three-Stage Pressure Regulated Circuit
- Remote Port Single-Stage Pressure Regulated Circuit
- Remote Port Two-Stage Pressure Regulated Circuit
- Dual-Pressure Circuit
- 2 Pressure Reducing Circuits
- Single-Stage Pressure Reducing Circuit
- Two-Stage Pressure Reducing Circuit
- 3 Pressure Holding Circuits
- Pressure Holding Circuit via Reversing Valve
- Pressure Holding Circuit via One-Way Valve
- Pressure Holding Circuit via Pilot Check Valve
- 4 Balancing Circuits
- Balancing Circuit via Sequence Valve
- Balancing Circuit via Pilot Sequence Valve
- Balancing and Pressure Holding Circuit
- Balancing Circuit via Pilot Check Valve and One-Way Throttle Valve
- 5 Pressure Relief Circuits (Pressure-Venting Circuits)
- Pressure Relief Circuit via Travel Valve
- Reversing Circuit via Two-Position Two-Way Valve
- Pressure Relief Circuit via Pilot-Oriented Pressure Relief Valve
- Pressure Relief Circuit via Three-Position Four-Way Reversing Valve (M-Type, Mid-Position)
- Pressure Relief Circuit via Three-Position Four-Way Reversing Valve (Y-Type, Mid-Position)
- 6 Buffer Circuits
- Buffer Circuit via Speed Regulated Valve
- Buffer Circuit via Pressure Relief Valve
- Speed Control Circuits
- 1 Throttle Speed Regulated Circuits
- Oil-Inlet Throttle Circuit via Throttle Valve
- Oil-Return Throttle Circuit via Throttle Valve
- By-Pass Throttle Circuit via Throttle Valve
- Oil-Return Throttle Circuit via Speed Regulated Valve
- Oil-Inlet Throttle Circuit via Speed Regulated Circuit
- By-Pass Throttle Circuit via Speed Regulated Valve
- Bidirectional Oil-Inlet Throttle Circuit via One-Way Throttle Valve
- Bidirectional Oil-Return Throttle Circuit via One-Way Throttle Valve
- Bidirectional Oil-Inlet Throttle Circuit via Two-Way Throttle Valve
- Bidirectional Oil-Return Throttle Circuit via Two-Way Throttle Valve
- Oil-Inlet Throttle Circuit via Back Pressure Valve
- 2 Fast-Speed Movement Circuits
- Differential Connection Circuit via One-Way Valve
- Differential Connection Circuit via Two-Position Three-Way Solenoid Valve
- 3 Speed Shift Circuits
- Fast and Slow Speed Connection Circuit via Travel Valve
- Speed Shift Circuit via Series Speed Regulated Valve
- Oil-Inlet Control Speed Shift Circuit
- Oil-Return Control Speed Shift Circuit
- Differential Connection Circuit via Two-Position Two-Way Solenoid Valve
- Differential Connection Circuit via Two-Position Three-Way Solenoid Valve
- Fast and Slow Speed Shift Circuit
- Speed Shift Circuit via Parallel Regulated Valve
- Oil-Return Control Speed Shift Circuit via Parallel Regulated Valve
- Bidirectional Speed Shift Circuit
- Directional Control Circuits
- 1 Reversing Circuits
- Continuous Reciprocating Motion Circuit via Two-Position Four-Way Solenoid Valve
- Continuous Reciprocating Motion Circuit via Three-Position Four-Way Solenoid Valve
- 2 Lock Circuits
- Lock Circuit via One-Way Valve
- Lock Circuit via Pilot Check Valve
- Lock Circuit via Three-Position Four-Way Solenoid Valve (O-Type, Mid-Position)
- Lock Circuit via Three-Position Four-Way Solenoid Valve (M-Type, Mid-Position)
- Multi-Cylinder Control Action Circuits
- 1 Sequence Action Circuits
- Sequence Action Circuit via Single Sequential Valve
- Sequence Action Circuit via Dual Sequential Valve
- Sequence Action Circuit via Pressure Relay
- Sequence Action Circuit via Travel Switch/Limit Switch
- Sequence Action Circuit via Joint Sequence Valve and Travel Switch/Limit Switch
- Sequence Action Circuit via Joint Pressure Relay and Travel Switch/Limit Switch
- 2 Synchronization Action Control Circuits
- Oil-Inlet Throttle Bidirectional Synchronization Circuit
- Oil-Return Throttle Bidirectional Synchronization Circuit
- Oil-Out Throttle Synchronization Circuit via Speed Regulated Valve
- Oil-Inlet Throttle Synchronization Circuit via Speed Regulated Valve
Part B: PLC Electrical Control Experiments
- PLC Programming Instructions and Ladder Programming
- Learning and Using PLC Programming Software
- PLC and Computer Communication
- PLC Applications and Optimization in Hydraulic Transmission Systems
This High-Performance Practical Hydraulic Drive and Controlled Trainer provides comprehensive and optimized hydraulic circuit training, offering students hands-on experience in designing, controlling, and troubleshooting hydraulic systems. It also includes advanced PLC control integration, making it ideal for both theoretical learning and practical applications in hydraulic engineering.
1.Motor Specifications:
Motor A:
Rated Power: 2.2KW
Rated Speed: 1420 RPM
Power Supply: AC 380V
Motor B:
Rated Power: 1.5KW
Rated Speed: 1420 RPM
Power Supply: AC 380V
2.Quantitative Gear Pump:
Rated Displacement: 7.8 cc/rev
Rated Pressure: 7 MPa
3.Variable Vane Pump:
Rated Displacement: 6.7 cc/rev
Rated Pressure: 7 MPa
Pressure Adjustment Range: 3-7 MPa
Dimensions:
1600 × 660 × 1800 mm (L × W × H)
These enhanced technical parameters ensure your hydraulic system operates efficiently, with robust motor performance, precise pressure control, and advanced monitoring capabilities.